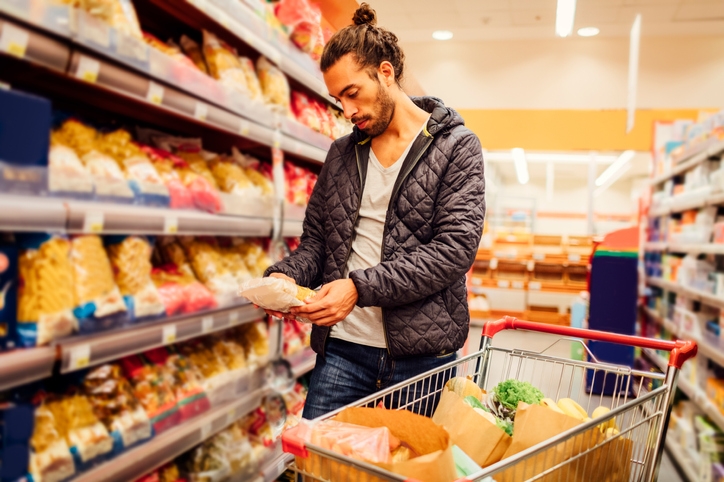
To assure the highest level of food safety possible for their customers, leading retailers have established requirements or codes of practice regarding foreign object prevention and detection. In general, these are enhanced versions of the standards established many years ago by the British Retail Consortium.
One of the most stringent food safety standards was developed by Marks and Spencer (M&S), a leading retailer in the UK. Its standard specifies what type of foreign object detection system should be used, how it must function to assure rejected products are removed from production, how the systems should “fail” safely under all conditions, how it should be audited, what records must be kept and what the desired sensitivity is for various size metal detector apertures, among others. It also specifies when an X-ray system should be used instead of a metal detector.
Foreign objects are challenging to find with conventional inspection practices because of their variable size, thin shape, material composition, numerous possible orientations in a package and their light density. Metal detection and/or X-ray inspection are the two most common technologies used to find foreign objects in food. Each technology should be considered independently and based upon the specific application.
Food metal detection is based on the response of an electromagnetic field at a specific frequency within a stainless steel case. Any interference or imbalance in the signal is detected as a metal object. Food metal detectors that are equipped with Fanchi Multi-scan technology enable operators to pick a set of up to three frequencies from 50 kHz to 1000 kHz. The technology then scans through each frequency at a very rapid rate. Running three frequencies helps make the machine close to ideal for detecting any type of metal you might encounter. Sensitivity is optimized, as you can choose to run the optimal frequency for each type of metal of concern. The result is that the probability of detection goes up exponentially and escapes are reduced.
Food X-ray inspection is based on a density measurement system, so some nonmetallic contaminants can be detected in certain situations. The X-ray beams are passed through the product and an image is collected on a detector.
Metal detectors can be used at low frequency with products that have metal in their packaging, but in most cases the sensitivity will be much improved if X-ray detection systems are used. This includes packs with metallized film, aluminum foil trays, metal cans and jars with metal lids. X-ray systems can also potentially detect foreign objects like glass, bone or stone.

Whether metal detection or x-ray inspection, M&S requires the following system features to meet its basic requirements.
Basic Conveyor System Compliance Features
● All system sensors must be failsafe, so when they fail they are in the closed position and trigger an alarm
● Automatic rejection system (including belt stop)
● Pack registration photo eye on the infeed
● Lockable reject bin
● Full enclosure between the inspection point and the reject bin to prohibit removal of contaminated product
● Reject confirmation sensing (reject activation for retracting belt systems)
● Bin full notification
● Bin open/unlocked time alarm
● Low air pressure switch with air dump valve
● Key switch to start the line
● Lamp stack with:
● Red lamp where on/steady indicates alarms and blinking indicates bin open
● White lamp indicating the need for QA Check (audit software feature)
● Alarm horn
● For applications where a higher level of compliance is requested, systems should include the following additional features.
● Exit check sensor
● Speed encoder
Failsafe Operation Details
To ensure all production is inspected correctly, the following failsafe features should be available to create faults or alarms to notify operators.
● Metal detector fault
● Reject confirmation alarm
● Reject bin full alarm
● Reject bin open/unlocked alarm
● Air pressure failure alarm (for standard pusher and air blast rejection)
● Reject device failure alarm (for retracting conveyor belt systems only)
● Exit Check pack detection (higher level compliance)
Please note all faults and alarms must persist after a power cycle and only a QA manager or similar high-level user with a key switch should be able to clear them and restart the line.
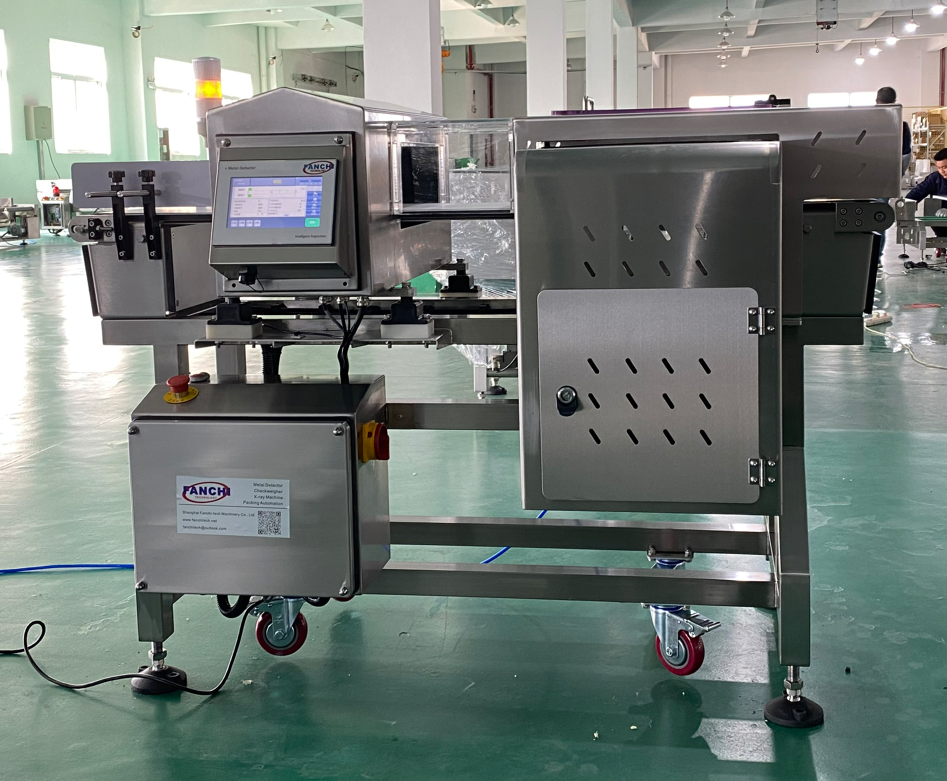
Sensitivity Guidelines
The table below shows the sensitivity required to comply with the M&S guidelines.
Level 1 Sensitivity: This is the target range of test piece sizes which should be detectable based on the height of the product on the conveyor and the use of an appropriately sized metal detector. It is expected that the best sensitivity (i.e. smallest test sample) is achieved for each food product.
Level 2 Sensitivity: This range should only be used where documented evidence is available to show that test piece sizes within the Level 1 Sensitivity range are not achievable due to high product effect or the use of metallized film packaging. Again it is expected that the best sensitivity (i.e. smallest test sample) is achieved for each food product.
When using metal detection in the Level 2 range it is recommended to use the metal detector with Fanchi-tech Multi-scan technology. Its adjustability, higher sensitivity and increased probability of detection will yield the best results.
Summary
By meeting the M&S “gold standard,” a food manufacturer can have the assurance that their product inspection program will provide the confidence that major retailers are increasingly insisting upon for the safety of consumers. At the same time, it also provides their brand with the best possible protection.
Want to know more about metal detection and X-ray inspection technologies that meet the Marks & Spencer requirements? Please contact our sales engineer to get professional documents, fanchitech@outlook.com
Post time: Jul-11-2022