
Noise is a common occupational hazard in food processing factories. From vibrating panels to mechanical rotors, stators, fans, conveyors, pumps, compressors, palletisers and fork lifts. Additionally, some less obvious sound disturbances can impair the performance of highly sensitive metal detection and checkweighing equipment. The most overlooked being earth/ground loops and electric motor drives.
Jason Lu, Technical Applications Support at Fanchi Technology, examines the cause and effect of these disturbances and the measures that can be implemented to reduce noise interference.
Many factors determine the theoretical sensitivity of a metal detector. Among them are the aperture size (the smaller the aperture, the smaller the piece of metal that can be detected), the type of metal, product effect, and the orientation of the product and contaminant as it passes through the detector. However, environmental conditions, such as airborne electrical interference – static, radio or earth loops – vibration, for example moving metal, and temperature fluctuations, such as ovens or cooling tunnels, may also affect performance.
Unique features like Noise Immunity Structure and digital filters which feature on the company’s digital metal detectors can suppress some of this interference noise, which may otherwise require reducing the sensitivity levels manually.
The main sources of electromagnetic interference and radio frequency interference include electric motor drives – for instance variable frequency drives and servo motors, motor cables not shielded correctly, two way radios, including walkie talkies, ground loops, electrical contactors and static discharge.
Ground loop feedback
The most widespread challenge Fanchi engineers encounter turns out to be quite a common issue in food factories. Particularly on end-to-end processing lines incorporating robots, bagging, flow wrapping and conveyors. The effects of electromagnetic interference can negatively impact the performance of metal detectors resulting in false detections, false rejections, and consequently increase food safety risks.
“Packaging machines such as flow wrappers and conveyor belts tend to be the biggest cause of ground loop issues due to worn out or loose fixings and rollers” says Jason.
Ground loop feedback occurs when any metallic parts in close proximity to the detector connect to make a conductive loop, for example an idle roller that has not been correctly insulated on one side of the frame notes Jason. He explains: “A loop forms which allows induced electrical current to flow. This in turn can cause a signal noise which disrupts the metal detection signal and can cause processing issues, such as false product rejects”.
Radio waves
The susceptibility of a metal detector to magnetic or electromagnetic interference is very dependent on its sensitivity and detection bandwidth. If one metal detector is transmitting a similar frequency to another in a busy factory environment, they are likely to cross talk with each other if positioned close together. To prevent this happening, Fanchi recommends spacing metal detectors at least four metres apart, or staggering the metal detector frequencies so they aren’t directly aligned.
Long and medium wave transmitters – such as walkie talkies – rarely cause problems. Providing they aren’t cranked too high or used in very close proximity to the metal detector coil receiver. For safety, keep walkie talkies operating at three watts or less.
Digital communication devices, for example smart phones, emit even fewer noise interferences, notes Jason. “It does depend how sensitive the coil unit is and again the proximity of the device to the metal detector. But mobile devices are rarely on the same bandwidth as processing equipment. So it’s less of an issue.”
Static troubleshooting
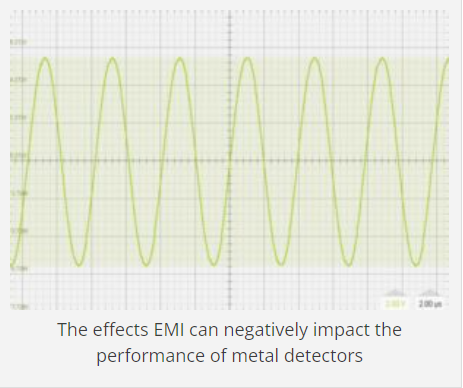
The effects EMI can negatively impact the performance of metal detectors
Any small movements in the mechanical construction of metal detectors which causes small vibrations can also trigger false rejects. Static electricity build up is more likely to occur on gravity and vertical metal detection applications if the pipework has not been earthed correctly, states Jason.
Locating a metal detector on a mezzanine floor can create potential issues. Notably more mechanical noise infractions, particularly from chutes, hoppers and conveyors. “Metal detectors that are phased to wet products are generally even more sensitive to this type of vibration and noise,” states Jason.
To ensure the most reliable performance and avoid vibration, all support structures and reject devices should be welded. Fanchi also avoids using anti-static belting material, as this too can reduce metal detector performance.
Finding the source of the problem quickly and accurately is critical, as ongoing interference on automated processing lines can cause service disruptions. Fanchi can deploy a sniffer unit to swiftly track the source of nearby EMI and RFI. Like an antenna, the white disc measures wavelengths and can swiftly located the source of the competing frequencies. With this information, engineers can shield, supress or alter the path of the emissions.
Fanchi also offers the option to upgrade to a high voltage oscillator. For extremely noisy production settings, including highly automated plants, this solution makes the Fanchi metal detector the dominant noise source.
User-friendly
Fanchi features like automated single pass learning and calibration can deliver an accurate system set-up within seconds and eliminate human errors. Additionally, built-in noise immunity structure – included as standard on all Fanchi digital metal detectors, can dramatically reduce the effects of external electrical noise, again resulting in fewer false product rejects.
Jason concludes: “It is impossible to completely eliminate noise interference in production environments. Yet, by taking these precautions and seeking expert guidance, our engineers can significantly reduce the EMI feedback and ensure metal detection performance and sensitivity is not compromised.”
Post time: Feb-28-2024